Green woodworking, using unseasoned timber, benefits from using nature as the factory to a greater extent than ‘conventional’ carpentry. Branches are used rather then requiring whole trees to be felled, and with less or no machine processing energy, glues and finishes. The craft often occurs in woodland near to the trees from which wood is sourced, increasing sensitivity to effects on the ecosystem, and providing an enviable place to work.
Bodging is a traditional green woodworking occupation, where chair components were made in the woods and exported to workshops where the complete chairs were assembled by furniture makers (called cabinetmakers in the UK).
Green woodworking has seen a recent revival due to its increased media coverage and the renaissance of hand tool woodworking in general.
Uses
- Furniture is a good fit for the scale and strength properties enabled by green-woodworking: chairs, stools
- Gardening tools like rakes
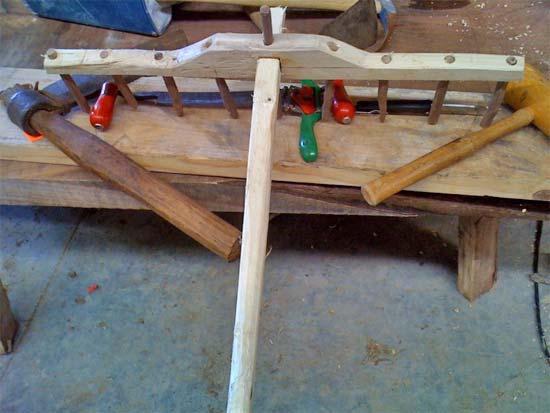
- Household items like firewood carriers, magazine-racks, shelves
- Carved spoons
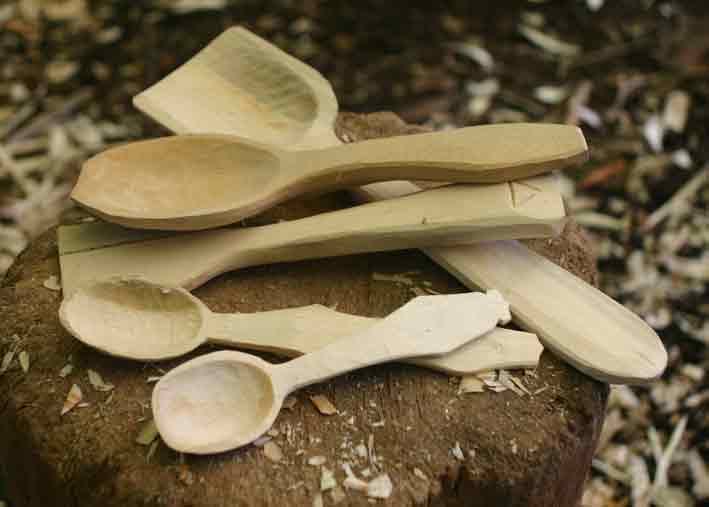
Processes
Green timber is softer than seasoned timber so hand or small power tools can be used rather than industrial machines. It can also be cleaved (split) along the grain rather than requiring sawing into planks. Green woodworkers try to use the natural shape and flexibility of branches in their designs, so can use them whole or cleft (split). Cleaving follows the grain and can be far stronger than planks where the sawing cuts through grain fibres; “like spring-steel compared to cast iron“, so smaller members are required.
Joints can be made without adhesives by exploiting the shrinkage that occurs as the members dry. Drier timber is used for the tenon resulting in it shrinking less than the encapsulating mortise so that the joint tightens as they dry.
If wood cannot be used when freshly felled it can be preserved for green woodwork by storing it in a water-filled trough or pond to maintain moisture.
More Information
- https://en.wikipedia.org/wiki/Bodging
- https://goingwiththegrain.org/what-is-green-woodwork/